Service and Support
RMI offer a comprehensive package of service support solutions, to suit your specific site needs.
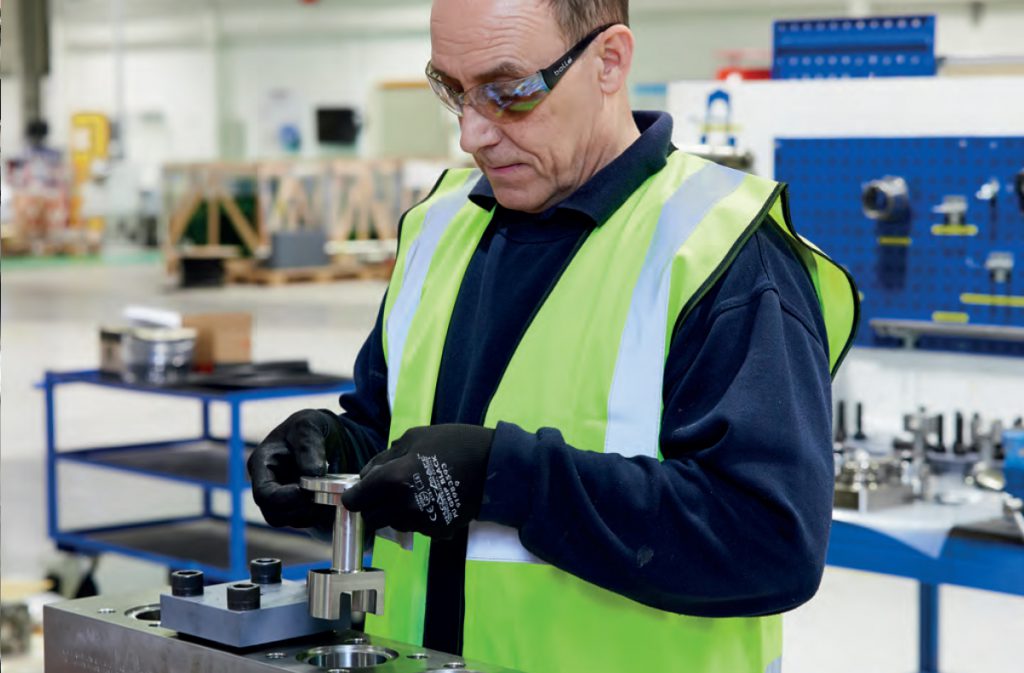
Design
Every high pressure pumping application deserves its own solution. RMI delivers this with its depth of in-house design expertise – built over more than a century of experience.
Total systems
In addition to designing our own range of premium quality high pressure pumps, we also design total systems for global mining and heavy industrial applications.
Latest design technologies
Our designers harness the latest technology tools in finite element analysis to validate pump performance and reliability, as well as computational fluid dynamics to maximise efficiency in our wetted components.
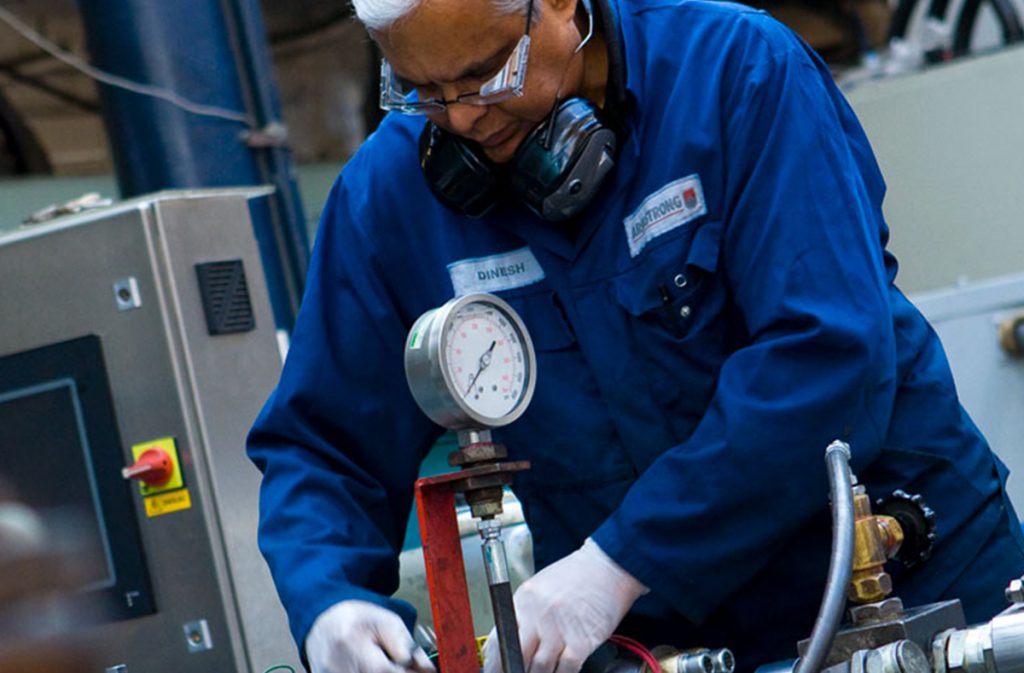
Testing
Assuring customers of quality and reliability, all RMI pumps undergo rigorous testing before delivery – conducted in-house at our manufacturing facility in Manchester, United Kingdom. Our local facilities in core markets including China are also equipped to test equipment after servicing, repairs or upgrades.
Test cells
Dedicated test cells put equipment and components through as many as two million pump cycles (up to 160 hours) in testing.
Testing capacity
Each cell can accommodate up to three RMI high pressure pumps, ensuring that extended periods of testing do not compromise our production rates.
Data driven
Temperatures, pressures, speeds and other indicators are measured, generating data that is carefully reviewed and analysed by our engineering team.
Detailed inspection
RMI’s inspection team tests new components extensively against conformance criteria before incorporation in our designs. Any improvements are thoroughly tested before being introduced to the market.
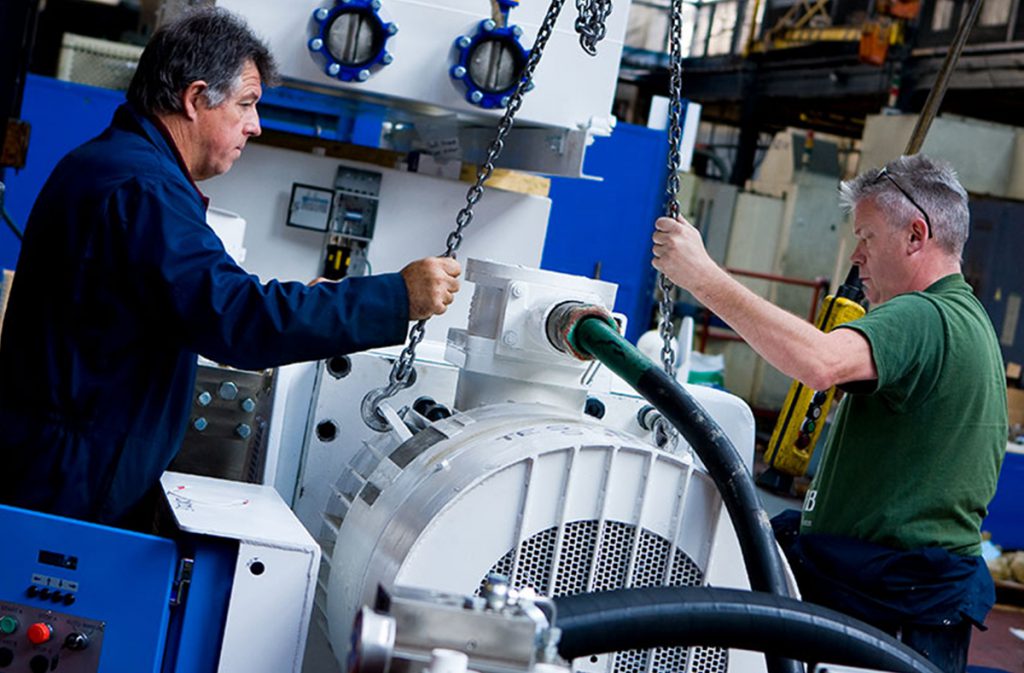
Commissioning
RMI’s experienced teams give customers the support they need to put their high pressure pumping solutions to work quickly and seamlessly.
In-factory testing
All RMI’s equipment is put through extensive testing in our dedicated test beds before shipping, ensuring rapid commissioning and optimal performance.
Local and on-site services
Wherever in the world our customer’s site is located, our expert technicians can assist to fast-track the commissioning process for early productivity. Our local presence in core markets including China allows quick access to customers’ operations.
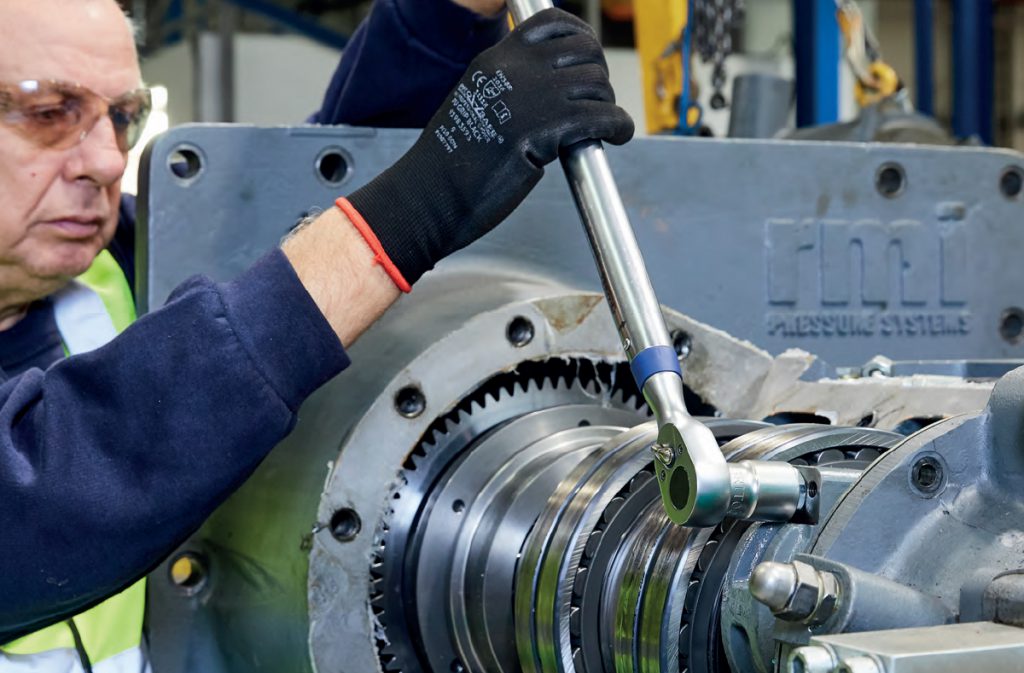
Service/Repairs
RMI prioritises the uptime of its pumping solutions, to give customers the productivity they need to achieve the lowest cost of equipment ownership. This means having service support resources available locally, and planning ahead to optimise uptime. Our fully equipped workshops in core markets including China ensure the highest standards of workmanship.
Health checks and monitoring
We offer both maintenance visits and annual service contracts that can be tailored to suit individual site needs and budget.
Manage performance
We offer advice on performance management to enable planned, predictive maintenance that delivers system reliability.
Emergency on-site repairs
For complete reassurance, our team of service engineers can be on call for on-site emergency repairs just when you need us.
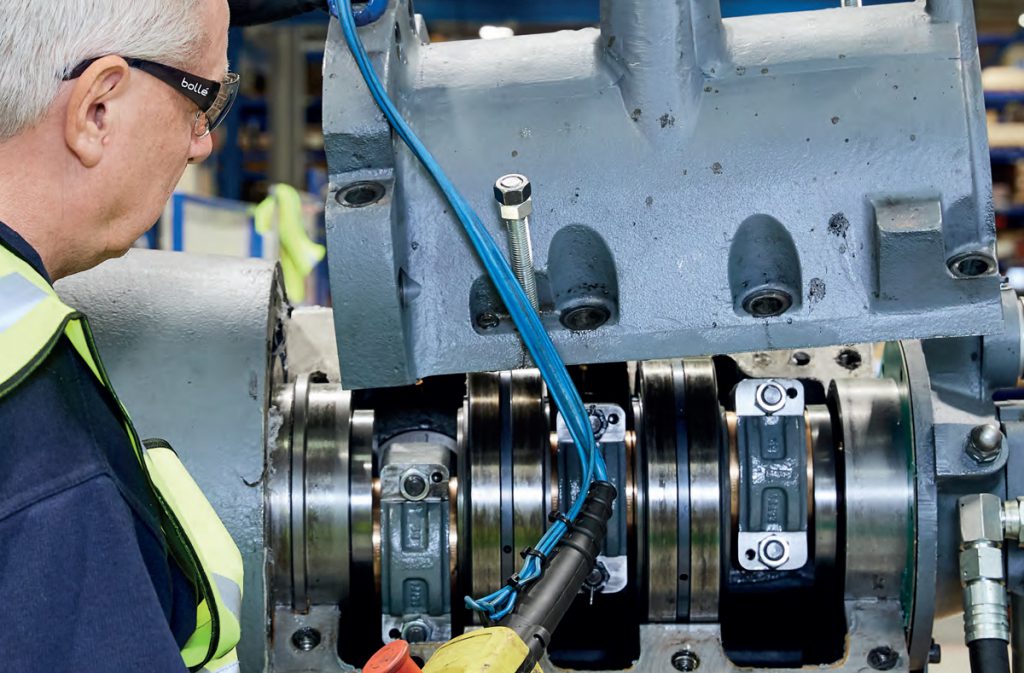
Overhauls/Upgrades
At RMI, our overhauls are another opportunity to upgrade our customers’ high-pressure pumping solutions with the latest materials and technology.
Continuous improvement
RMI strives to improve the quality, reliability and performance of our products, using state-of-the-art design, materials and technology. For customers, this means getting the very latest components with the highest specifications – effectively upgrading your equipment during each overhaul.
Productivity
Our quality pumping solutions allow extended operating periods between upgrades, making sure customers achieve enhanced productivity from their equipment.
Longevity
These upgrades facilitate longer working life, for the lowest total cost of ownership.
Planning ahead
For peak performance and longevity, RMI helps customers schedule and implement a structured maintenance plan, with kits and modules to streamline the process.
On-site assessment
Our expert team of engineers can conduct a full on-site assessment of your equipment needs, with technical recommendations to enhance performance and reliability.
Service centres
In addition to conducting on-site upgrades, RMI has conveniently located service centres where your equipment can be maintained off-site. These centres offer full strip-down reports and detailed quotations, giving you complete control of costs at all times.
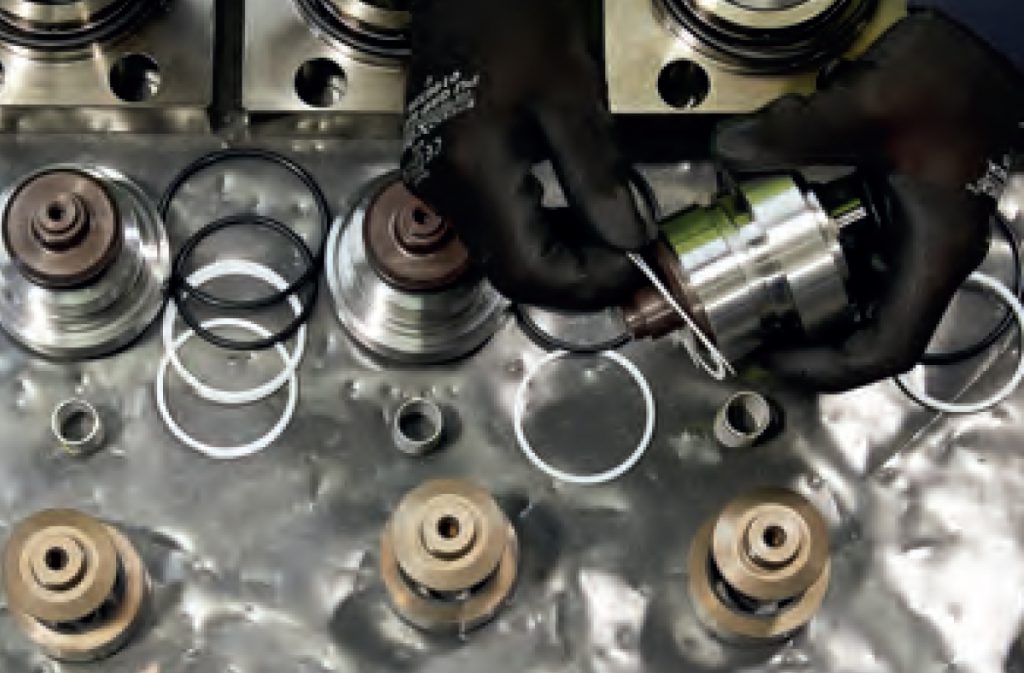
Genuine Spare Parts
RMI ensures that customers have easy access to the latest genuine spare parts that comply with our high standards of quality manufacture.
Modules and kits
We have designed modules and kits of our genuine spares, to streamline your maintenance and upgrades – helping keep your pumps running at optimal performance for longer.
Reduced inventory
With our modules and kits, customers can rest assured that they have the right set of components on hand for whenever they are required. This reduces customers’ spare parts inventory, and avoids potential delays waiting for deliveries.
Latest generation components
RMI is continuously improving the design and materials of its genuine spare parts. Each overhaul therefore translates into an effective upgrade for our customers.
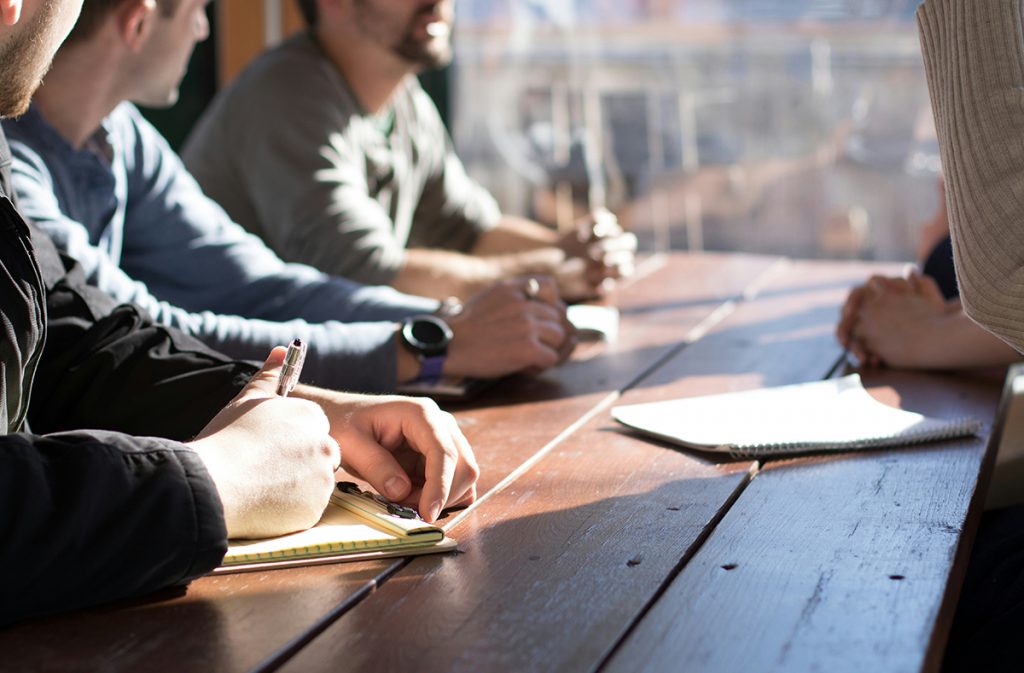
Training
The right expertise is a cornerstone of RMI’s success, and we readily share knowledge with our customers on safe and effective operation and maintenance.
Site training
RMI can train site engineers and operators to ensure that they are equipped to operate the equipment safely and execute routine maintenance tasks.
Brochures

System Upgrades and Servicing Brochure
NEED OUR HELP WITH A PROJECT?
Send us some details and we will have one of our experts contact you a.s.a.p