With its modern workshop and assembly facilities in Shanghai, RMI Pressure Systems ensures customers in China of OEM-standard upgrades, commonly referred to as overhauls in the Chinese market – with an extensive stockholding of genuine spare parts to allow quick turnaround times.
Sabrina Zhang, Director for Aftermarket Sales, Services and RMI Operations in China, said that the company’s MA-certified facility was a vital part of RMI’s localisation strategy. The facility can conduct full strip-down and rebuild services, with upgraded spares and components adding wherever possible to the performance and lifespan of RMI high pressure reciprocal pumps.
She emphasised that RMI is continuously improving its components, so that customer’s pump systems can be fitted with the latest technology and material during routine maintenance. This turns a regular overhaul into an actual upgrade – contributing to product quality and longevity.
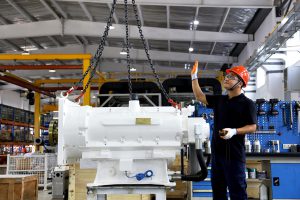
Continuous component improvements by RMI lead to routine maintenance becoming a genuine upgrade for enhanced product quality and longevity
Legacy
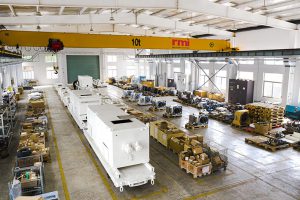
RMI’s Shanghai facility excels in full strip-down and rebuild services, enhancing performance and lifespan of high-pressure pumps
“With our legacy of over 30 years of supplying and supporting our pump stations in China’s underground mines, our brand has a strong reputation locally,” she explained. “Our Shanghai facility further enhances our upgrade and spares offering, ensuring uptime and productivity.”
The history of RMI goes back over a century, giving the company a unique depth of expertise in pump technology. This has allowed the company to develop innovative maintenance schedules to improve performance and reliability. Over a typical six-year cycle, RMI recommends three different grades of overhauls or upgrades: A, B and C.
“Grade A is the intervention that we recommend at the end of the first and second years, which usually aligns with the annual completion of a longwall panel,” she said. “This involves the replacement of various wet end parts, and this can be done underground, without needing to move the pump system to surface.”
Spare part kits
The consumable components that need replacing at this stage include lubrication oils, filter elements, seals, O-rings and packing. Valve chest springs, ceramic rams and unloading valve cartridges are also among the parts replaced. RMI streamlines the maintenance process by making all relevant spare parts available in dedicated kits – each designed to contain everything necessary for the specific grade of overhaul.
At the end of the third year, a Grade B upgrade is recommended, which comprises a full rebuild. This can be conducted in-house by those customers who have their own maintenance facilities and skills; alternatively, RMI undertakes this upgrade at its own workshop. RMI pump stations are delivered with training materials and detailed product manuals for owners who can conduct rebuilds in-house. Additional components replaced at this stage include con rods, ram holders and the oil pump.
“This first rebuild allows our pump systems to operate consistently at peak performance, and we then recommend annual Grade A upgrades again for the following two years,” said Zhang. “This takes the system into its sixth year, at the end of which we recommend a Grade C upgrade – also an intensive rebuild.”
Service exchange
Similar to Grade B, the Grade C intervention also includes additional aspects such as replacing the pump module and the oil cooler assembly. She highlighted that RMI can provide customers with a service exchange offering – which is particularly valuable for those customers who do not have their own replacement units. To ensure minimal downtime, RMI designs and manufactures an identical pump for the customer, ready for installation when their existing unit is removed for a rebuild.
“This saves time, and allows operations to continue without undue disruption,” she said. She noted that customers are aware of the importance of regular maintenance interventions, and are open to the advice provided by RMI’s experienced technical service engineers – who visit customer sites to track machine condition and performance.
“Our service engineers produce a detailed report after each visit, including feedback on any aspects that may need attention in the near future,” she said.
Maintenance agreements
To make full use of RMI’s support in China, some mines have signed long-term overhaul agreements for a three-year period, she noted. The arrangement means that RMI collects a customer’s pumping system from the mine and transports it to the Shanghai workshop for a full strip-down and rebuild. The customer is involved in the process, to consider the results of a technical inspection and choose between an overhaul or replacement. RMI then conducts the Grade A servicing on site after each longwall panel is completed.
“This ensures the customer of high levels of reliability and uptime for better productivity, while also controlling their capital and maintenance costs in advance,” said Zhang.
The local availability of RMI’s genuine spare parts has been considerably enhanced by the Shanghai facility, she pointed out. Quick access to components has been a cornerstone of RMI’s strategy in China, and urgent parts can now be delivered to customers within three to four days. The company’s technical service centres, located close to main mining areas, allow technical service engineers to reach customers within two hours. There are also key consumables stored at the service centres for immediate access.
Recent Comments