When a steel rolling mill in Italy was looking to enhance the quality of its product while improving overall efficiency, it turned to a partnership of metallurgical plant solutions company Primetals Technologies and high-pressure pump specialist RMI Pressure Systems.
The mill decided to invest in new descaling equipment – with a view to raising quality standards while lowering overall energy and water costs. According to Kathryn Poke, RMI’s general manager for Europe, the Middle East and Africa (EMEA), the company designed a bespoke solution based on its established Trimax Series of reciprocating plunger pumps.
RMI Pressure Systems designed a bespoke solution based on its established Trimax Series of reciprocating plunger pumps
“Engineered to order like all our solutions, we designed the system to suit the project requirements,” said Poke. “With the Trimax pump at its heart, the specialised system for the mill included controls, nozzles and headers to ensure reliable and efficient operation.”
RMI was required to provide a pump which could deliver hydraulic power at multiple pressures, using a variable speed drive and engineered nozzles. The result was a system capable of producing flow rates from 50 up to 670 litres per minute, at pressures up to 1,000 bar.
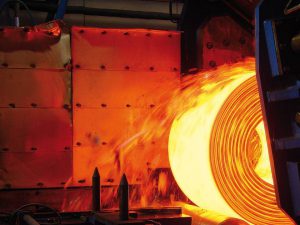
RMI Pressure Systems helps steel manufacturers improve overall efficiency in steel descaling operations (Image: Primetals Technologies)
“The technical design of descaling equipment is an exact science,” she explained. “This requires precision nozzle design and high hydraulic pressures calculated to deliver the best descaling results for a variety of steel variants, at minimum cost and maximum efficiency.”
The variable speed drive and engineered nozzles ensured that the system delivered controlled hydraulic pressure and precision impact, while consuming less energy and water. The system was performance-tested, confirming its robust design and manufacture – which would underpin its reliability and uptime. The lower installation and maintenance costs resulted in a payback period of less than two years.
RMI managing director Joe Keenan highlighted the value for customers of pump manufacturers moving beyond a focus on discreet products and into the systems space.
“Customers are increasingly looking for solutions and not just products,” said Keenan. “This contract illustrates how RMI’s custom-design capability allows us to build fit-for-purpose solutions with our pumps as a central component.”
He noted that the trend is toward OEMs gaining more specialised knowledge about how pumps are applied in specific applications, so that they can augment their offerings with other componentry, accessories and technology. This allows the customer to source more of their operational equipment from a single supplier, reducing the risk and resources associated with integrating and maintaining these different elements in-house.
RMI Pressure Systems is a global leader in high pressure and high volume fluid pumping stations, with over a century’s experience in designing, manufacturing and supporting this technology. With a product development and manufacturing hub in Manchester, England, RMI Pressure Systems has operations in the US, China, India and Australia. It also serves markets in Europe, the Middle East and Africa. Its in-house research and development capability drives the continuous innovation of its products and solutions.
Recent Comments